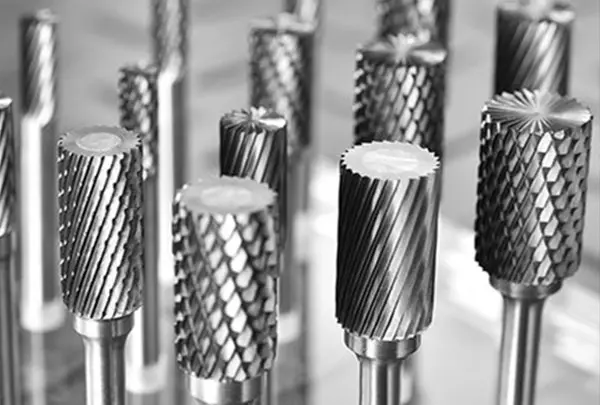
How To Choose The Right Carbide Burrs?
Carbide burrs, also known as carbide rotary burrs are used with high-speed electric mills or die grinders to process metal, wood, plastics, etc. Carbide rotary burrs are widely used in machinery, automobile, shipbuilding, chemical industry, craft carving, and other industries. Selecting the right carbide burr for your project is of great importance. There are several methods for choosing a high-quality tungsten carbide rotary burr.
Shapes of tungsten carbide rotary burrs
The shape of the carbide rotary burr should be determined by the shape of the workpiece. When processing the internal arc surface, a semi-circular burr or round burr (small diameter workpiece) should be used; when processing the inner corner surface, triangular burrs should be selected; when processing the inner right angle surface, a flat burr and square burr can be selected. When the flat burr is used to cut the inner right angle surface, it is necessary to make a narrow surface (smooth edge) without teeth close to one of the inner right angle surfaces, so as to avoid damaging the right angle surface.
Tooth thickness of carbide rotary burrs
The thickness of burr teeth should be determined according to the allowance size of the workpiece, machining accuracy, and material properties. The coarse tooth carbide burr is suitable for machining workpieces with large allowance, low dimensional accuracy, large form and position tolerance, large surface roughness value, and soft material; otherwise, fine-tooth carbide burr should be selected. When used, it should be chosen according to machining allowance, dimensional accuracy, and surface roughness required by the workpiece.
Sizes of carbide burrs
The size and specification of cemented carbide rotary burr should be selected according to the size of the workpiece and machining allowance. When the machining size is large and the allowance is large, cemented carbide rotary burr with a large size should be selected, or a tungsten carbide rotary burr with a small size should be selected instead.
Tooth patterns of tungsten carbide burrs
The tooth pattern of tungsten steel carbide rotary burrs should be chosen according to the properties of the workpiece material to be processed. When filing aluminum, copper, soft steel, and other soft materials, the best choice is a single tooth (milling teeth) carbide burr. The single tooth pattern file has a large front angle, small wedge angle, large chip holding groove, hard chip blocking, and sharp cutting edge.
After knowing the methods and principles of selecting high-quality tungsten carbide rotary burr, it turns to understand its application and advantage. Cemented carbide rotary burr is an essential tool in industrial processing and it is also a favorite tool for craft lovers. As teeth of industry, cemented carbide rotary burr covers various benefits and is largely used in many fields.
1. Can process cast iron, cast steel, carbon steel, alloy steel, stainless steel, copper, aluminum, and other metals, and marble, jade, bone, and other non-metallic. Processing hardness can reach HRA ≥ 85.
2. It can basically replace a small grinding wheel with a handle without dust pollution.
3. High production efficiency. Processing efficiency is ten times higher than that of a manual burr and nearly ten times higher than that of a small grinding wheel with a handle.
4. Good processing quality and high finish. It can process all kinds of high-precision mold cavities.
5. Long service life. Its durability is 10 times higher than that of a high-speed steel tool and 200 times higher than that of a small grinding wheel.
6. Easy to master, easy to use, safe, and reliable.
7. Comprehensive processing costs can be reduced dozens of times.
The service life of tungsten steel carbide rotary burrs is another element for product performance and a key point that Procurement and users both pay attention to. There are some instructions for prolonging the service life of cemented carbide rotary burr. In order to prolong the service life of cemented carbide rotary burr, the following rules must be observed:
1. It is not allowed to use new tungsten steel carbide rotary burrs to process hard metal;
2. It is not allowed to process quenched materials with tungsten steel carbide rotary burrs ;
3. Forgings and castings with hard skin or sticking sand can only be processed with a semi-sharp carbide burr after being ground off by a grinder;
4. Use one side of the new carbide burr first, and then use the other side after the first surface is blunt,
5. During processing, always use a wire brush to remove chips on carbide burr teeth,
6. Cemented carbide rotary burr should not be overlapped or stacked with other tools;
7. It is not advised to use tungsten steel carbide rotary burrs so fast, in order to avoid abrasive carbide burrs.
8. Cemented carbide rotary burr should be kept away from water, oil, or other dirt;
9. It is not allowed to file soft metal with a thin carbide burr.
10. When using cemented carbide rotary burr, force should not be too large, so as not to break the carbide burr.
Konetool has specialized in producing cemented carbide rotary burrs for more than ten years. Products adopt CNC automatic production equipment and use a modern management mode. Product quality is checked at all levels. The quality of all products exceeds that of similar enterprises. Therefore, it is highly praised by our customers.