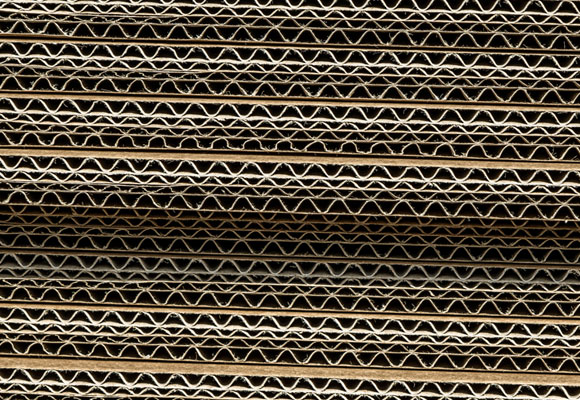
How Is Cardboard Made?
Cardboard mainly refers to corrugated cardboard which is widely used in our daily life, such as packaging. It is sturdy, lightweight, and versatile, making it extremely suitable for delivering, displaying, and protecting products. Despite its ordinary appearance, manufacturing cardboard is very complicated. How is cardboard made? Generally, cardboard is made in a large machine called a corrugator. In this article, we’ll briefly introduce the manufacturing processes of corrugated cardboard boxes.
Raw materials
Typically, a piece of cardboard has three layers – an outer liner, an inner liner, and a fluting medium. The outer liner is also known as Kraft paper which is a type of paper made from chemical pulp and manufactured in the kraft process. Kraft paper is strong and has high tensile strength. The raw material of Kraft paper needs to be softwood with long fibers, such as Pines, Firs, and Spruces. Depending on the type of tree, Kraft paper looks different in color.
Unlike Kraft paper, inner liners are mainly made from hardwood with short fibers, such as Oak, or recycled paper. They are cheaper and have lower quality. The fluting medium layer is made from either softwood or hardwood. Both are fine.
Apart from the above materials, there are other raw materials are required in the production of corrugated paper. For example, corn starch glue is used as the adhesive to stick fluting medium layers to the liners.
How Is Cardboard Made?
Generally, papers are created from wood at a paper mill. Then, rolls of paper are sent to a corrugating plant to be processed into corrugated cardboard boxes.
- Pulping
Pulping is aimed at breaking down the structure of wood chips and turning them into fibers. Fibers can then be made into pulp. The process starts with the debarking and chipping of trees. These wood chips are then put through either mechanical pulping or chemical pulping (aka the Kraft process).
Chemical pulping applies a chemical cooking method to separate the fibers from the lignin. Sulphite and sulphate are two common types of chemical cooking that perform perfectly in the separation and reduction of lignin. However, sulphate is relatively more popular as it uses sodium sulphate to increase the strength of the pulp. The chemical pulping process results in a dark brown color. Or if a white Kraft is required, a bleaching process during the chemical pulping process can achieve the expected result. In fact, these days most paper used for manufacturing boxes is made from recycled waste.
Mechanical pulping however utilizes a grinding method. By grinding wood chips against a revolving disk or stone grinders to break down the fibers. This method removes little lignin, thus reducing the paper quality. However, it is cheaper and generates higher output than chemical pulping.
- Paper Making
Next, how to convert the pulp into paper or board? Despite the different types of paper, the paper-making process remains the same. The pulp should experience a process named beating during which it is pounded and squeezed by a beating machine. At this stage, filler materials should be added to the pulp to adjust the opacity, including chalks and clay. Besides, sizing is another important added material that can influence how inks react with the paper. Frequently-used sizing materials include rosins, starch, and gums.
After the beating process, the wood pulp will be fed into a paper-making machine, also called a Fourdrinier machine. This machine has a wire mesh that is designed for squeezing the pulp with rollers. A suction device is installed underneath to drain water. Now, a piece of paper is initially formed. The paper is then pressed between steam-heated rollers and wool-felt blankets to remove any remaining water. Finally, the finished products are rolled for the following processes.
- Corrugating
Rolls of Kraft paper are then delivered to a plant called corrugating or converting plant. At this plant, there are large machines known as corrugators that are specifically applied to manufacturing corrugated cardboard. As we mentioned before, some paper is used as the fluting medium, while others are used as liners. To form a piece of corrugated cardboard, liners are glued on each side of the fluting medium.
To start, load a roll of the corrugated medium and two rolls of the liner into the corrugator. The liners will be glued to the fluting medium later. The corrugating rollers used for fluting are covered with ridges, also called flutes. After these corrugating rollers are heated, the medium layer passes between them to form crinkly flutes. Then, this medium layer passes through the glue station for gluing. After the glue is applied to the fluting medium, the liners can adhere to the medium layer. A large piece of corrugated cardboard is finished. However, to get a suitable size for making boxes, large pieces will finally be cut into box blanks in proper sizes by slitter scorer blades and cut-off knives.
Konetool is a reliable supplier and manufacturer of corrugated slitter scorer blades and cut-off knives made from top-grade tungsten carbide. If you’re interested in our knives, please feel free to request a quote.